We visit the mills of Yorkshire, courtesy of Woolmark
For A/W14, French fashion house Louis Vuitton presented a 60s-inspired tapestry of intricate woven knits, in mini-dresses, roll necks, and printed jersey, quickly becoming one of the most easily recognised shows of the season. Lesser known however is that 17 of these woven designs can be credited to Bower Roebuck, a quiet mill nestled in the Yorkshire hills. Roebuck plays a silent, artisan hand in a host of leading fashion houses, including Dunhill, Burberry and Ralph Lauren. They manufacture 390,000 metres of cloth per annum, equating to 6,000 pieces.
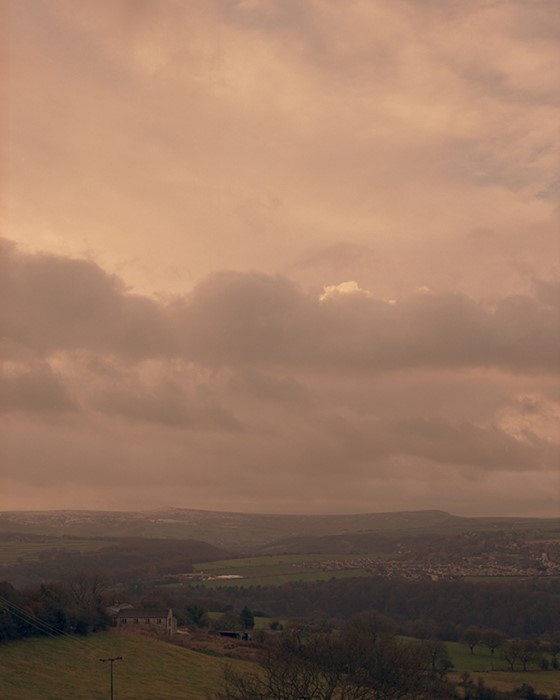
Like Scotland, Yorkshire has a long history with the wool industry. Bower Roebuck sits alongside Clissold, Abraham Moons and Hinchliffe Yarn Spinners, dating back to the 18th century. “Trading was done on a bartering system,” recalls Robert Hinchliffe. “Cloth went down on packhorses to Staffordshire where the emerging pottery industry was evolving. Woollroen cloth was bartered for pottery goods, which were then brought back up and sold off. That was the origin of the business.” Indeed, much of the prosperity of Britain can be credited to wool – an industry that helped lay the foundations for the British Empire.
"The textile industry in Yorkshire has weathered a tough storm, from the political fights of the 19th century to the financial battles of recent decades"
However, the textile industry in Yorkshire has weathered a tough storm, from the political fights of the 19th century to the financial battles of recent decades. “There are interesting articles in the archives about families defending their mills,” remembers Hinchliffe. “There were some serious battles and cracked skulls on both sides.”
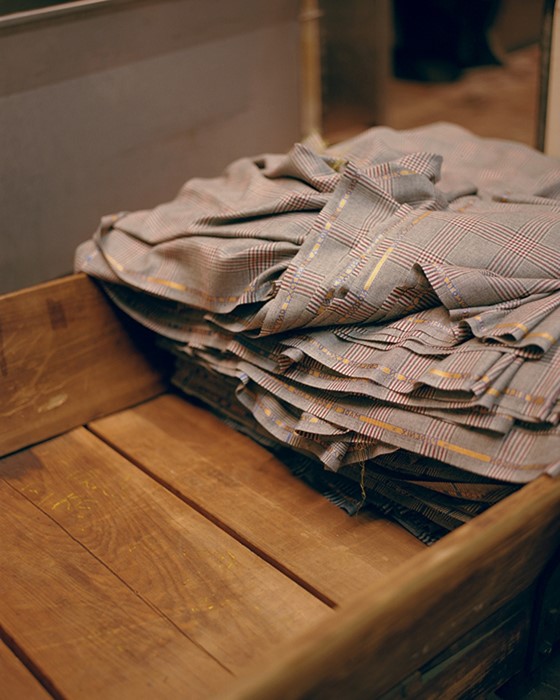
In 2014, wool is currently on top of its game, driven by a public desire to know the quality and origin of clothing, alongside a new pride in fashion houses to support the British textile industry. “Many international companies will not buy fabric, unless it reads Made in Britain,” advises Ronald Hall. There is an astonishing level of work and attention to detail that goes into wool production, such as at WT Johnson and Son’s finishing mill, a world leader in fabric finishing, which works through over 100,000 metres of fabric every week. At Roebuck, there is a team dedicated to scrupulously hand-mending imperfections, laboriously picking through every metre that travels through the doors.
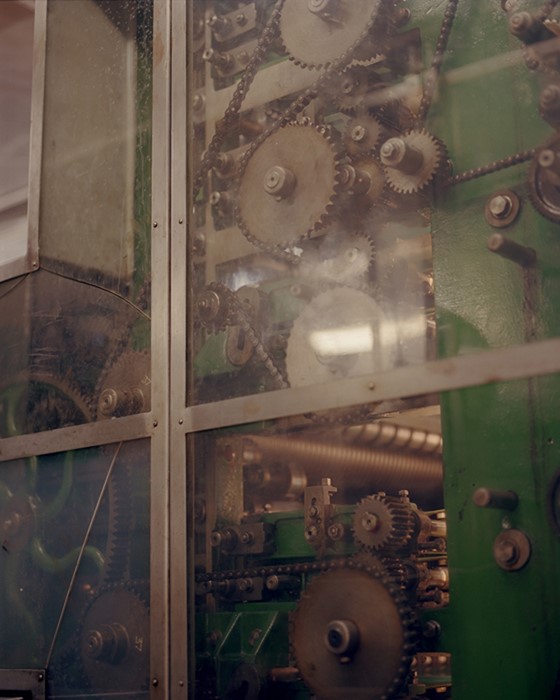
The rebirth of the prestigious International Woolmark Prize has also played a great hand in public awareness of the industry. The historic competition which famously launched the careers of Karl Lagerfeld and Yves Saint Laurent back in 1954 was reestablished in 2012, aiding designers including Agi & Sam and Sibling. The Woolmark company is also currently involved in the Loom to London program, an initiative which aims to create relationships between young designers and UK manufacturers. Designers currently involved include Agi & Sam, Katie Eary and Craig Green while Christopher Raeburn, Lou Dalton and Richard James are all part of Woolmark's London Collection: Men Designer Collaborations project, the results of which will be seen at the menswear shows in January. "Working in partnership with Woolmark has allowed us to develop a better understanding of the opportunities when working with wool," comments Christopher Raeburn. "It has led to the development of our best-selling hybrid hoodie – a truly innovative garment for S/S15 which links functionality and fabric technology."
The International Woolmark Prize Menswear Final will take place in January 2015.
Words by Mhairi Graham